TIME & MOTION STUDY – Industrial Engineer & Consultant Services
We Help Manufacturing Companies Improve Process and Productivity – Reduce Business Costs – We Help Improve Work Methods, Set Time Study Standards.
.
WE WATCH PEOPLE WORK – Improve Production & Efficiency
.
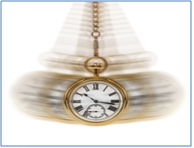
Problems You May Have:
- Job Taking Too Long
- Poor Method of Assembly
- Picking / Kitting Taking Too Long
- Not Meeting Customer Deliveries
- Want To Reduce Your Business Costs
- We Can Help You Implement Your Ideas
.
Services We Offer:
.
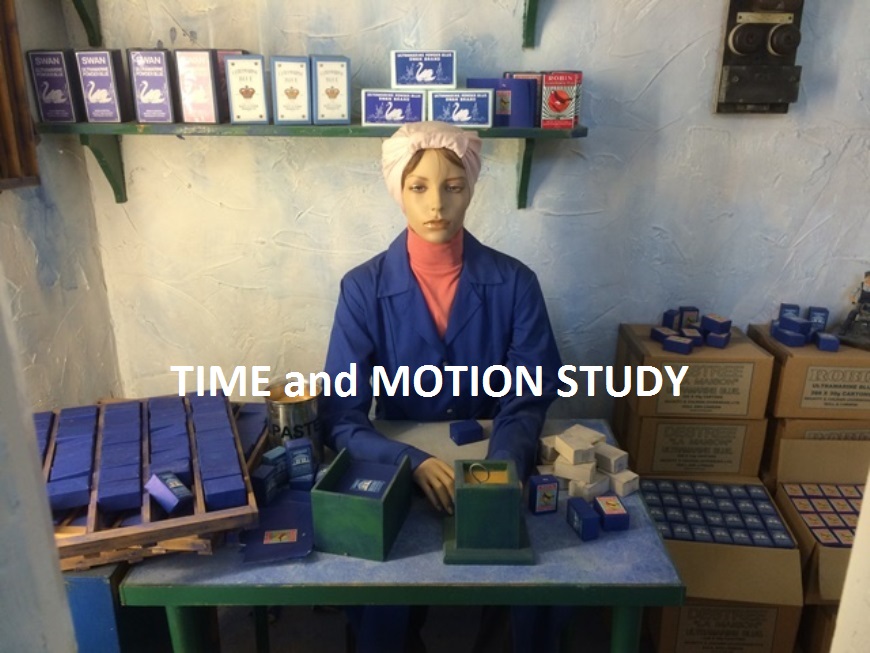
Time and Motion Study:
Time & Motion Study Expertise Is In “Watching People Work”
We have over 30 years experience, knowledge and expertise in Work Study and Time & Motion Study Principles. And help business reduce costs
We look for “Non-Value Waste”. Waste in Time – Inventory – Movement – Waiting – Over-processing – Scrap – Rejects – OEE – Machine down-time.
We give hands-on-help:- introduce “Best Practice Methods” Using LEAN Manufacturing Principles and methodologies to improve process, productivity and Reduce Costs
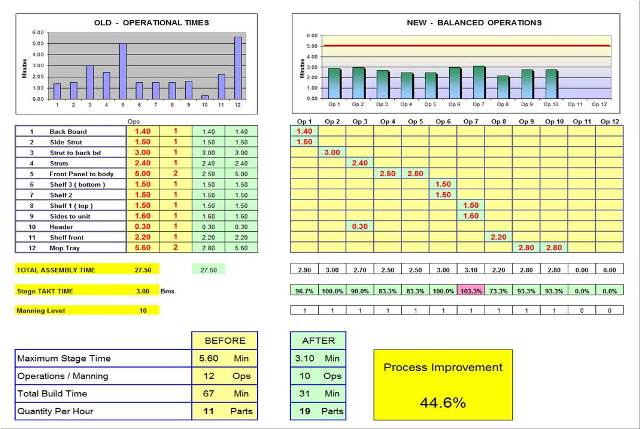
.
Cycle Time Measurement:
We Can Help You With:
- Time Operations
- Balance Flow Lines
- Organise Bench Layouts
- Best Practice Process Methods
- Bench-mark Operation Times & Targets
.
We can establish a “STANDARD TIME” for an operator to carry out a job… Using a Stop Watch, NOT Mobile Phone…
- We analyse peoples work rate (some people work slowly, others briskly) The BSI100 Standard Rating Scale is applied to produce the right time for a work operation…
- TAKT TIME and TARGETS can then be applied to Bench-mark operations… Costing, Production Planning and planning for on-time deliveries…
- LEAN Line Balancing will balance production through-put – To improve manning, production and reduce costs
We Help People In Manufacturing Improve Processes & Reduce Costs
.
Atherton Management Services Ltd
.
Please Contact Us, We Are Happy To Help:
We’ve generated for our clients between £50k and £2.0M per project
For over 30 years we’ve designed and implemented “Business Improvement” Projects.
Please Contact Us, tell us your issues – tell us how you would like to improve your business.
Please Contact Us:- UK – 07300 788 486 – or by E-Mail