QUALITY IMPROVEMENT – Engineer & Consultant Services
WE HELP Manufacturing Companies with Quality Improvement Engineering & Quality Awareness We Can Help:- Process Improvement & Reduce Costs
.
WE IMPROVE PROCESSES, PRODUCTIVITY, QUALITY – REDUCE COSTS
.
WHY IS QUALITY IMPORTANT IN MANUFACTURING and in BUSINESS:
- You realise that there is nothing worse than bad service.
- It takes a long time to get a customer
- But ONE mistake to lose them
CUSTOMERS EXPECT QUALITY – NOT Once, but Every-Time – Quality is the key to your customers satisfaction… “Quality Counts – If You Don’t Get It Right, Someone Else Will”
.
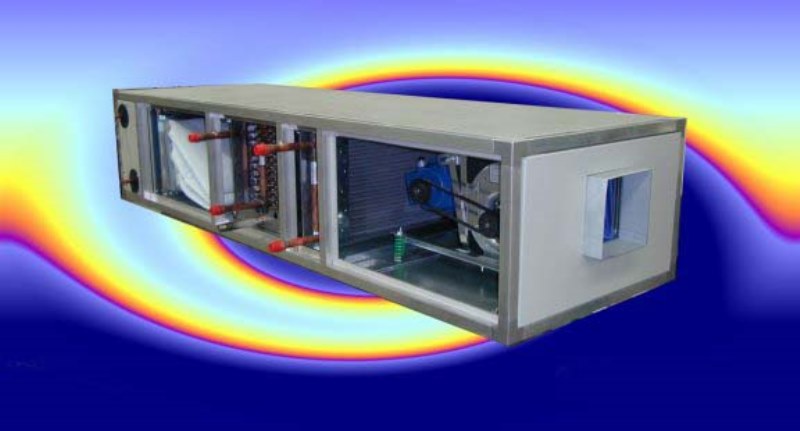
Customers Want:
- 1.RIGHT PRICE
- 2.QUALITY at 100%
- 3.BEST SERVICE at 100%
- 4.DELIVERY When the Customer Wants It
Customer Complaints, NCR’s and “Human Error” Will lose you customers… These have to be tackled “Head On”
.

Commitment To Quality:
- Design OUT Possible Rejects
- Design OUT Complicated Designs
- Design OUT a Complicated Process
- Design OUT the “Human Error” Factor
- Design IN Standardisation & Reduce Variation
- Design IN Simple Product Design and Process
.
Services We Offer:
.
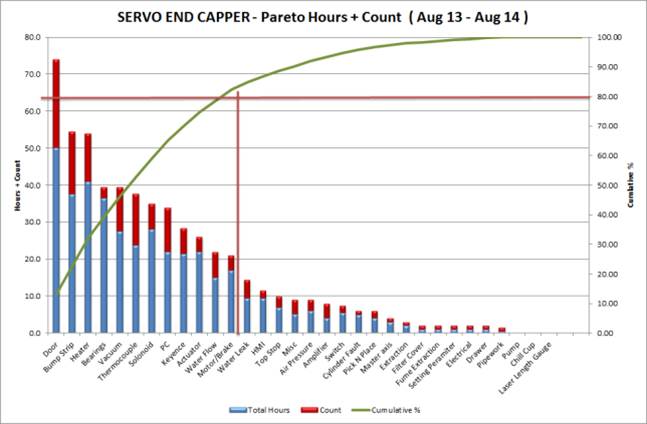
LET’S ASK SOME QUESTIONS:
What Is Your Biggest Headache At Work?
- In meetings, do you get the same issues day after day?
- What is the cost of poor quality issues – human errors?
- What is the cost of stoppages – down-time – rejects?
- What is the cost to the business of lost production?
- What Ideas Do You Have and Would Like To Implement?
.
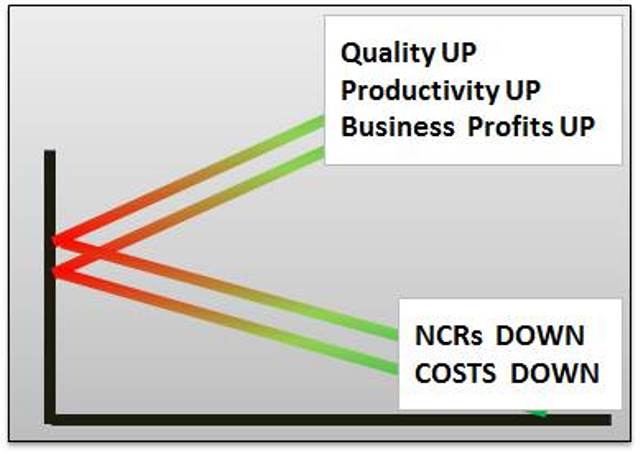
We Can Help You Improve Quality To Reduce Stress;
- 1.Analyse NCRs & KPIs
- 2.Analyse Customer Complaints
- 3.Analyse By Using Pareto Charting
- 5.Put Right Things That Cause You Grief
- 5.When Quality Goes UP – COSTS GO DOWN
- 6.When Quality Goes UP – Company Growth Goes UP
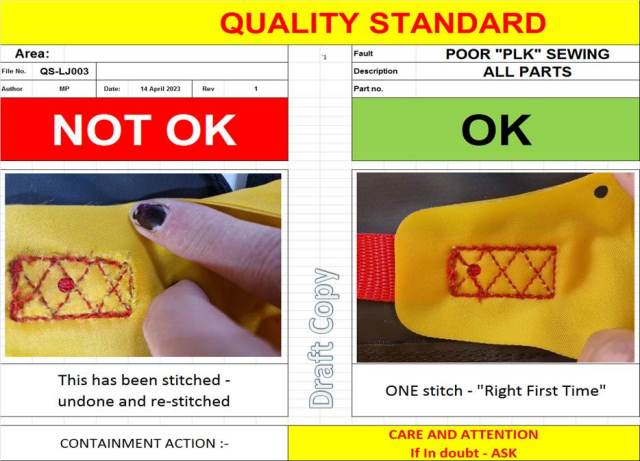
.
Manufacturing Work Instruction & Procedures: THE KEY TO QUALITY
Procedure Writing – Work Instructions – Quality Awareness Standards in manufacturing are vital to eliminate “Human Errors” Poor Quality, Lost Profit.
.
Many companies don’t use Work Procedures:-
- So, wonder why quality is not met and rejects are produced.
.
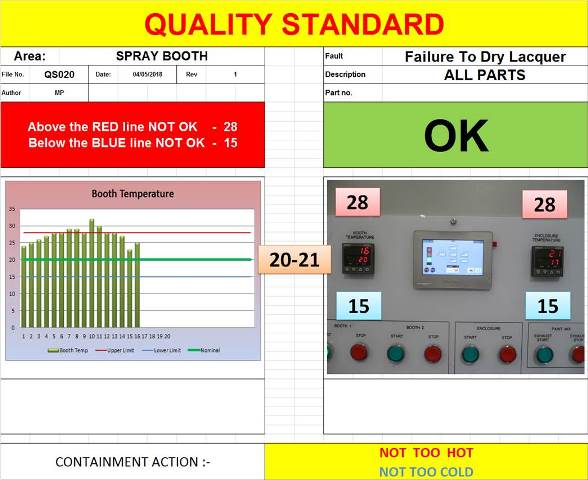
We Write SIMPLE Procedures: In Simple English to be understood
- Standard Op Procedures – will improve operator performance
- Quality Awareness Standards – will eradicate poor quality issues
- Operator Training – will eradicate operator mistakes and rejects
- With a 100% quality product – you retain customer satisfaction
- Management knows ‘what the customer wants’ – But do the workforce?
- We Write Quality Procedures – Eradicate NCRs and “Human Error”
.
We are that “independent extra pair of eyes”
Find Out How To Improve Quality and Reduce Costs
.
We Help People In Manufacturing Improve Processes and Reduce Costs
.
Atherton Management Services Ltd
.
Please Contact Us, We Are Happy To Help:
We’ve generated for our clients between £50k and £2.0M per project
For over 30 years we’ve designed and implemented “Business Improvement” Projects.
Please Contact Us, tell us your issues – tell us how you would like to improve your business.
Please Contact Us:- UK – 07300 788 486 – or by E-Mail